News center
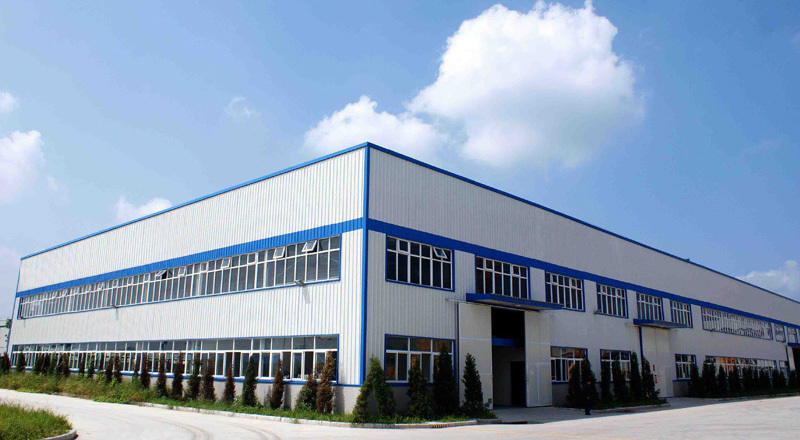
Precautions for stamping parts
1. Both semi-automatic and manual punching machines must be equipped with a dual hand brake switch, and it is strictly prohibited to press the switch by foot or by one hand. 2. After adjusting the machine for high impact and normal stamping, close the sound barrier box (except for the packaging of product 8065 during inspection). 3. During continuous stamping, employees are not allowed to pick up products by hand within 1 meter of the punching machine. 4. When technicians use the mold adjustment machine, they can only debug it by one person, not two people. 5. The technician can only adjust the machine and deliver materials outside the machine, with a distance of no less than 1M. 6. When erecting the mold, it is necessary to tighten the screws and stop the machine for 4 hours to check if the screws are loose.
2023-03-29
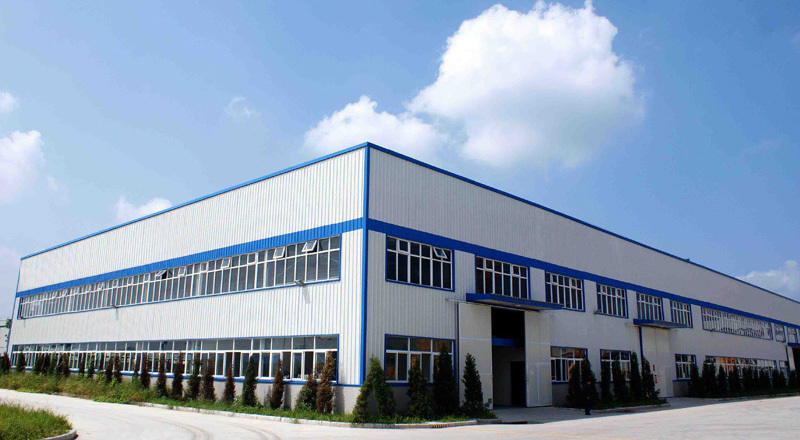
Application of Characteristics of Stamped Parts
Stamped parts are production techniques that utilize the power of conventional or specialized stamping equipment to directly deform the sheet metal in the mold, thereby obtaining a certain shape, size, and performance of product parts. Sheet metal, molds, and equipment are the three elements of stamping processing. Stamping is a method of metal cold deformation processing. So, it is called cold stamping or sheet metal stamping, abbreviated as stamping. It is one of the main methods of metal plastic processing (or pressure processing) and also belongs to material forming engineering technology. 50% to 60% of Universal's steel is made of sheet metal, with the majority being finished products that have been stamped and pressed. The body of a car, radiator fins, steam drum of a steam boiler, shell of a container, iron core silicon steel sheets of motors and electrical appliances are all stamped and processed. There are also a large number of stamping parts in products such as instruments, household appliances, office machines, and storage containers. Stamping is an efficient production measure that adopts composite molds, with the exception of multi-station progressive molds. It can complete multiple stamping technology operations on a single press and complete the automatic generation of materials. Fast production speed, long rest time, low production cost, collective production capacity of hundreds of pieces per minute, loved by many processing plants. Stamped parts, castings, and forgings have the characteristics of being thin, uniform, light, and strong. Stamping can produce workpieces with reinforcing ribs, ribs, coils, or flanges that are difficult to manufacture with this familiar hand diameter, in order to improve its rigidity. Due to the rejection of rough molds, the workpiece accuracy can reach the micrometer level, with high accuracy and consistent specifications, and can be punched out with holes, protrusions, etc. In actual production, process tests similar to the stamping process are commonly used, such as deep drawing performance tests, bulging performance tests, etc., to inspect the stamping performance of materials, in order to ensure the quality of finished products and high qualification rates. In addition to forming thick plates with a hydraulic press, stamping equipment usually uses a viscous press. Focusing on the modern high-speed multi-station viscous press, setting up equipment configuration such as uncoiling, product collection, and delivery, as well as mold storage and rapid mold replacement placement, and using computer French tube bundles, a passive stamping production line with high production rate can be formed. Under the condition of producing dozens or hundreds of stamping parts per minute, completing stamping and production processes in a short period of time often results in personal, equipment, and quality issues. Therefore, safety production in stamping is a crucial issue
2023-03-29
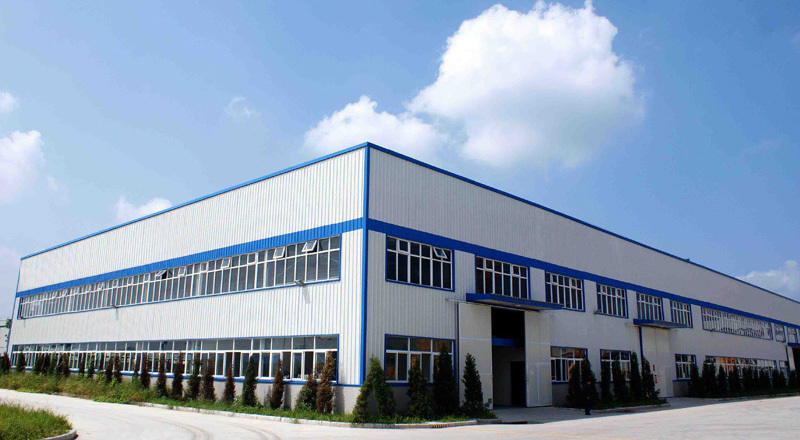
60% to 70% of the world's steel is made of sheet metal, most of which is stamped into finished products. The body, chassis, fuel tank, radiator plates of automobiles, boiler drums, container shells, motors, electrical appliances, and iron core silicon steel sheets are all stamped and processed. There are also a large number of stamping parts in products such as instruments, household appliances, bicycles, office machinery, and household utensils. Compared with castings and forgings, stamped parts have the characteristics of being thin, uniform, light, and strong. Stamping can produce workpieces with reinforcing ribs, ribs, undulations, or flanges that are difficult to manufacture by other methods to improve their rigidity. Due to the use of precision molds, the workpiece accuracy can reach the micrometer level, with high repeatability and consistent specifications, and can be punched out with holes, protrusions, etc. Stamping machine cold stamping parts generally do not undergo cutting processing, or only require a small amount of cutting processing. The precision and surface state of hot stamping parts are lower than those of cold stamping parts, but they are still better than castings and forgings, and the cutting amount is less. Stamping is an efficient production method that uses composite molds, especially multi-station progressive molds, to complete multiple stamping processes on a single press, achieving fully automatic production from strip uncoiling, leveling, punching to forming and finishing. High production efficiency, good labor conditions, low production costs, typically producing hundreds of pieces per minute. Stamping is mainly classified by process and can be divided into two categories: separation process and forming process. The separation process, also known as punching, aims to separate the stamped part from the sheet metal along a certain contour line while ensuring the quality requirements of the separated section. The surface and internal performance of stamping materials have a significant impact on the quality of stamping products, requiring accurate and uniform thickness of stamping materials; The surface is smooth and clean, without spots, scars, scratches, surface cracks, etc; Uniform yield strength without obvious directionality; High uniform elongation; Low yield strength ratio; Low work hardening.
2023-03-29
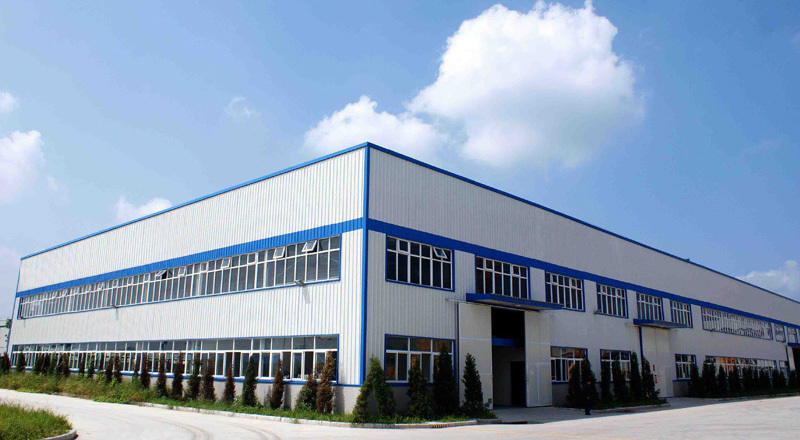
What are the characteristics of stamping parts processing?
The processing of stamping parts is based on the premise of low material consumption. The parts are lightweight and have good stiffness, and after plastic deformation of the sheet metal, the internal organizational structure of the metal is improved, thereby increasing the strength of the stamping parts. Stamped parts processing has relatively high dimensional accuracy, with uniform and consistent dimensions of the same module, and good interchangeability. No further mechanical processing is required to meet general assembly and usage requirements.
2023-03-13
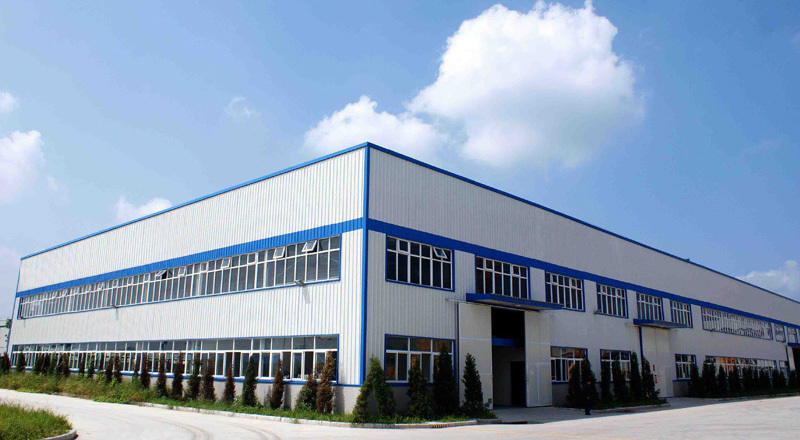
What are automotive hardware stamping parts
Automotive hardware stamping parts are one of the essential parts in automotive manufacturing. It includes various covering parts, decorative parts, fasteners, etc., and its usage on the car accounts for more than 10% of the total vehicle mass. The precision of stamping parts is generally required to adapt to the characteristics of large production batches, so the productivity of the stamping process is very high; At the same time, due to the large force exerted on the material during stamping, there are high requirements for the strength and toughness of the material; Additionally, it is required that the mold structure be simple and cost-effective.
2023-03-13
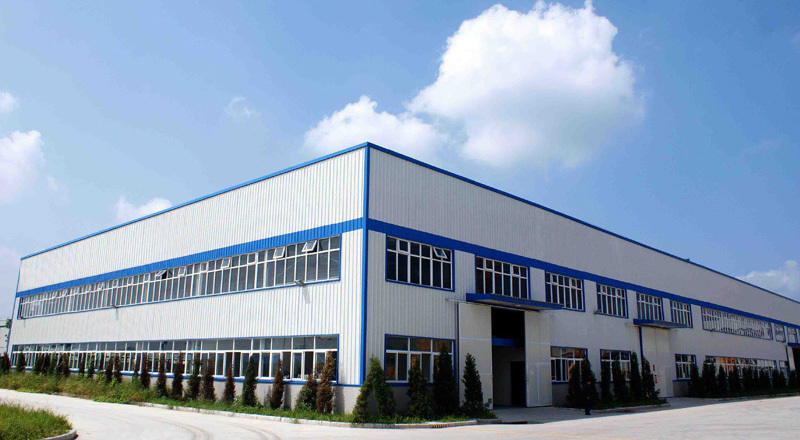
Advantages and disadvantages of single process mold structure
The rationality of the structure of cold stamping mold design plays a crucial role in the success of producing precision hardware components. Even a simple set of mold components can reach dozens of types, so their accuracy cannot be underestimated during design. What kind of mold structure was chosen at the beginning of the design? Is it a pre mold structure (i.e. the concave mold is installed on the lower mold base)? Is it an inverted (reverse) mold structure (i.e. a convex mold installed on the lower mold base)? Or choose a single process mold structure? Should we choose a composite mold structure? This is a topic worth in-depth discussion in front of every mold worker.
2023-03-13